In the first blog of this series, Continuous Manufacturing: A Pharmaceutical Application for DEM, we looked at how direct compression is one of the most effective methods to maximize the efficiency of manufacturing pharmaceutical tablets. This is because it is the simplest and most economical method of producing tablets and requires less processing steps than other techniques. However, not all problems related to direct compression tablet manufacturing have been resolved. Direct compression can produce surface imperfections in a tablet through chipping or capping, and tablets may delaminate while being ejected from a die. Another problem that can arise is that active pharmaceutical ingredient particles (APIs) may accumulate on the upper and lower punches after repeated compaction cycles through a process known as punch sticking.
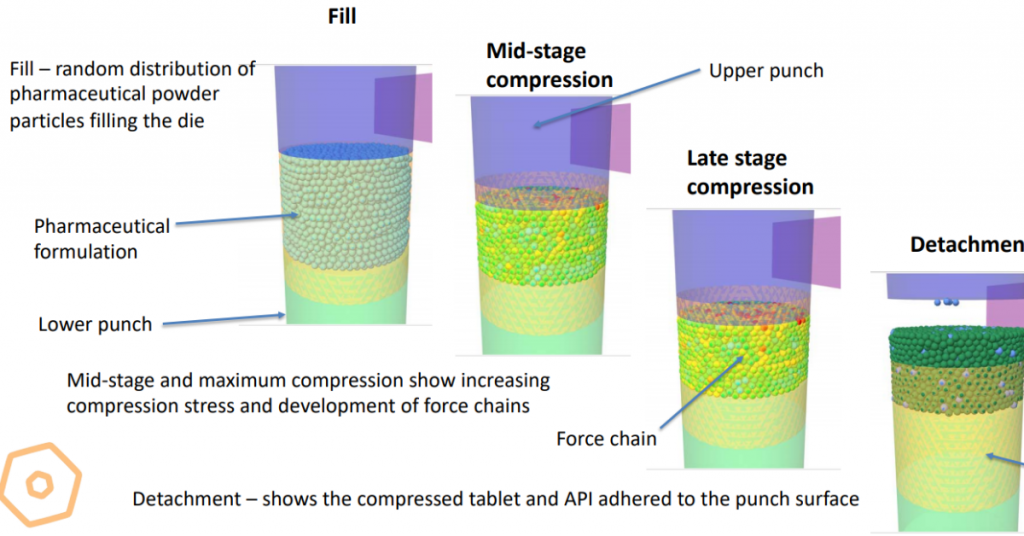
Factors Affecting Punch Sticking
Punch sticking occurs when API particles’ adhesion to the punch surfaces is stronger than the particles’ bonds to the surface of the tablet. There are numerous factors that affect punch sticking such as: particle and punch surface adhesion, micromechanical processes during a compression cycle, the amount of API in the formulated powder, and tablet detachment processes. These problems can affect product quality, require halting manufacturing to clean machinery, interfere with manufacturing efficiency, and result in financial losses. Coupi is working to help pharmaceutical companies understand these problems and explore ways to mitigate them using Coupi’s discrete element method (DEM) die compaction model.
Mitigating Issues with Coupi’s Die Compaction Model
In the model, formulated powders containing APIs and excipients rearrange during compression until they lock in place (packing) and when compression stresses exceed the particles’ yield stress they deform at their contacts. Cohesive and adhesive bridge bonds form between particles, between particles and punch, and between particles and die wall surfaces during deformation. Coupi’s double punch die tablet press model consists of an upper punch, lower punch, and cylindrical die. The die is filled with a formulated pharmaceutical powder of API and excipient particles. As the upper and lower punches approach each other, the particles rearrange and form force chains within the particle aggregate. Eventually particles lock up, force chains are destroyed, and when particles experience high stress they undergo significant deformation at their contacts forming bridge bonds. On unloading, the tablet is ejected, the upper plunch withdrawn, and the tablet detaches from the punches and is transported to a collection bin. When the upper punch detaches from the tablet, some API may stick to the punch depending on the adhesion and cohesion between the particles, the punch, and the die wall. Our model has been calibrated using measured adhesion/cohesion values for two formulated powders and has been used to create punch sticking risk maps that correlate well with punch sticking measurements. One of the first applications of the model was to assess and predict the risk of punch sticking. To simulate this process we used our Polyphysica DEM software to develop a mechanistic model of punch sticking processes.
In the figure above, API are shown in light blue and excipients in green. The tablets were manufactured through direct compression. This is done by filling a die with a formulated powder and compressing the powder in order to bond the powder particles together into a tablet. Then the punches (A and B) were withdrawn and the tablets pushed to the top of the dies by the lower punches. No API stuck to the surface of punch A, while a single API stuck to Punch B. The only difference between the two simulations is that the API-punch adhesion ratio for punch B is slightly larger than for punch A (1.3 for punch A and 1.4 for punch B).
The force plots for punch A and punch B tell the story. As the punches are withdrawn from the tablet, a tension force develops in the API bond with the punch (red data curve in the plot) and between the API and its three excipient particle bonds on the tablet surface (gold, blue and green curves). As the punches pull away from the tablets the tension forces increase until one of the API bonds attached to both punch A and tablet fails at the its contact with the tablet (blue) causing a further increase in tension between the API particle and punch A. However, the other two API bonds with the tablet do not break, so eventually the API bond to punch A fails and the API particle remains in contact with the tablet. For punch B, all three bonds between the API particle and the tablet fail (around 0.27 s) and the API particle remains stuck on the punch. The tension in the API bond with punch B then decreases to gravity force only.
This die compaction model has been used to examine the process of API punch sticking for multiple runs to determine the rate at which API can accumulate. The figure above shows the number of particles sticking to a punch at one, six, and ten compression cycles. The majority of particles sticking to the punch are API with some few excipient particles that are effectively pulled along with API. These results are in qualitative agreement with measurements.
Coupi Paves the Way to Improved Product
Coupi simulations of direct compression tablet creation are a useful way to evaluate tablet manufacturing operations, predict punch sticking risk, and examine tablet properties to help improve and optimize operations. In doing this, we help companies improve their product while saving time and money. Our simulations don’t end with die compaction though, we also simulate the feeder operations that drive powders into the tablet presses. If material is not fed properly, it could lead to issues further down the line in the manufacturing process. How well the feeder performs affects the concentration of API in formulated pharmaceutical powders and may reduce the quality of the final product.
If you or your company are interested in learning more about Coupi’s work, we offer free consultations. Contact us here.
Stay tuned for the next blog post in this series where we dive into the science of modeling feeders using Coupi’s Polyphysica DEM software.